The Logistics of Delivery: How Fulfillment Makes the Supply Chain Move
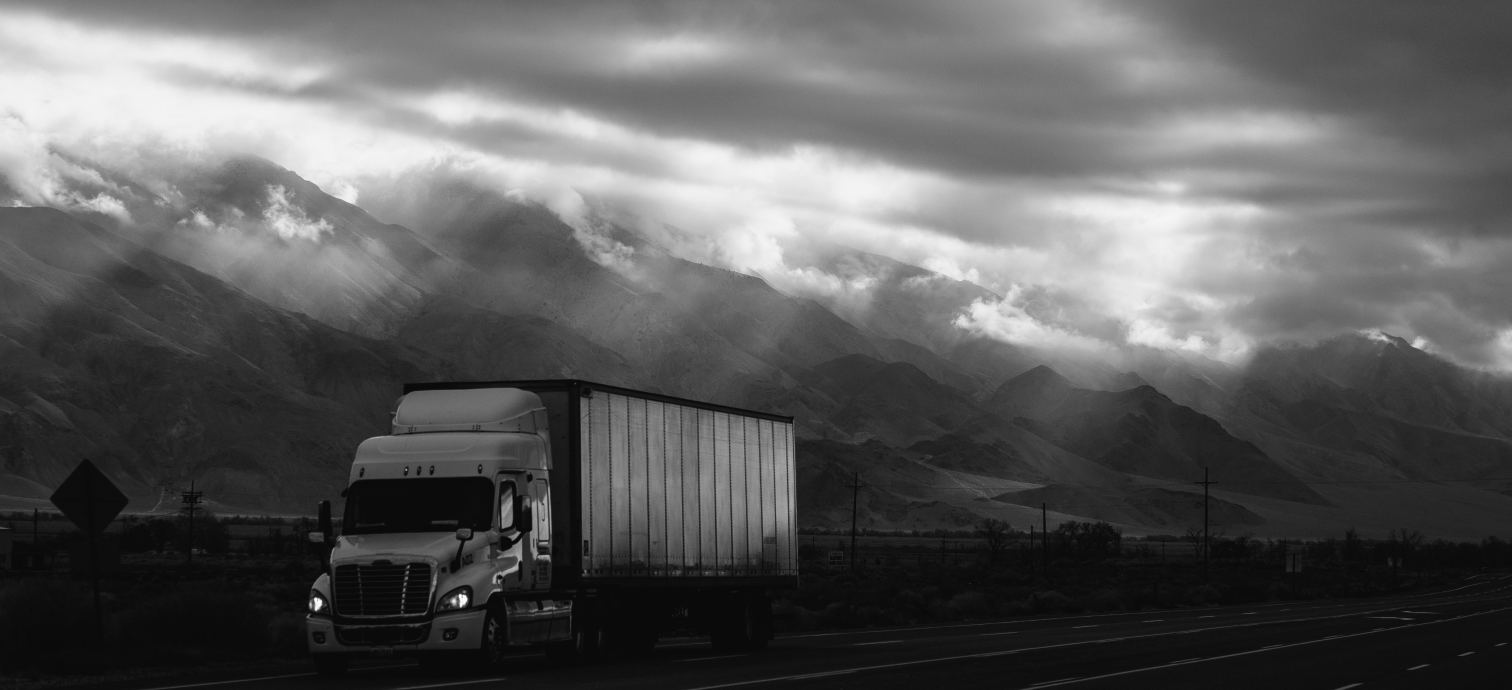
Fulfillment in logistics refers to the process of receiving, processing, and delivering orders to customers. It involves managing the entire order fulfillment process, including inventory management, order processing, picking and packing of products, and shipping.The ultimate goal is to ensure that customers receive their orders accurately and on time, so it is a critical aspect of the supply chain that has a significant impact on profitability and competitive advantage.Let’s discover a bit more!
Fulfillment Process
The fulfillment process is the backbone of the logistics industry. It is the process of receiving, processing, and delivering orders to customers, and it is critical for ensuring that businesses can deliver their products to customers quickly and efficiently. The fulfillment process is broken down into four main components: order processing, inventory management, picking and packing, and shipping.
Order Processing
This phase involves receiving orders from customers and inputting them into the system. It includes verifying payment, checking inventory levels, and confirming the order details. Once the order is verified, it moves onto the next step.
Inventory Management
This is the process of tracking inventory levels and ensuring that there is enough stock to fulfill customer orders. This phase involves monitoring inventory levels, tracking incoming shipments, and replenishing stock as needed. Effective inventory management is crucial for ensuring that orders can be fulfilled quickly and accurately.
Picking and Packing
This step is about physically selecting the products from the warehouse and packing them into boxes for shipment. This phase is critical for ensuring that orders are accurate and that products are protected during shipping. It also involves labeling and preparing the shipment for the next phase.
Shipping
It involves preparing the shipment for delivery and handing it off to the carrier, including the verification of the shipping address, choosing the carrier, and printing shipping labels. Once the shipment is handed off to the carrier, the fulfillment process is complete.
Key Components of Fulfillment in Logistics
- Warehouse Management: Managing the physical storage and movement of products within a warehouse (inventory levels, organizing products, and optimizing the layout of the warehouse) to minimize movement and improve efficiency.
- Transportation Management: It involves coordinating the movement of products from the warehouse to the customer, from selecting carriers to tracking shipments to ensure that they are delivered on time.
- Inventory Management: Effectively managing the flow of products in and out of the warehouse is essential. You should always monitor inventory levels, track incoming shipments, and replenish stock as needed.
- Order Management: This includes order processing, tracking, and fulfillment. Effective order management is critical for ensuring that orders are fulfilled accurately and on time.
- Customer Service: Good customer service improves customer satisfaction and loyalty, which might help to drive sales and improve profitability. This includes providing timely and accurate information to customers, addressing customer complaints and concerns, and providing support throughout the fulfillment process.
Benefits & Challenges of Fulfillment in Logistics
Pros
- Efficient fulfillment in logistics helps to improve the overall customer experience. By ensuring that products are delivered accurately and on time, customers are more likely to be satisfied with their purchase and return to do business with the company again.
- With optimized inventory management and efficient order processing, companies can reduce the time it takes to fulfill orders and get products to customers. This can help companies to meet customer expectations for faster delivery times, which can be a competitive advantage.
- Effective fulfillment in logistics can help businesses to reduce costs and improve profitability. By optimizing inventory levels, streamlining order processing, and improving shipping efficiency, businesses can reduce operating costs and improve their bottom line.
- By automating processes and streamlining workflows, you will increase efficiency and productivity, which will help you to reduce errors and improve accuracy, while also enabling employees to focus on other tasks that add value to the business.
Difficulties
- One of the main challenges of fulfillment in logistics is managing inventory levels. Businesses must keep track of their inventory levels to ensure that they have enough products on hand to fulfill customer orders, while also avoiding excess inventory that can tie up capital and lead to waste.
- Businesses must be able to quickly adapt to changes in demand and adjust as demand for products can fluctuate rapidly, making it difficult for businesses to keep up with orders.
- Returns and cancellations can be a major challenge for businesses. You must have systems and processes in place to manage returns and cancellations efficiently, while also minimizing the impact on your bottom line. REVER might be a key solution for your business.
Best Practices for Fulfillment in Logistics
Fulfillment in logistics requires businesses to implement best practices that help to optimize operations and improve bottom line:
Optimize Warehouse Layout and Organization
It helps to improve the efficiency of fulfillment operations. By organizing inventory in a logical and intuitive manner, businesses can reduce the time it takes to pick and pack orders, while also reducing the risk of errors.
Implement Technology Solutions
Technology solutions such as warehouse management systems (WMS), transportation management systems (TMS), and order management systems (OMS) can help you to automate processes and improve efficiency. Reduce manual processes and improve accuracy by leveraging technology.
Focus on Continuous Improvement
Fulfillment in logistics is an ongoing process that requires continuous improvement. By regularly reviewing processes and procedures, businesses can identify areas for improvement and make adjustments to improve efficiency and reduce costs.
Monitor and Measure Performance
Measuring and monitoring performance is critical to improving. Businesses should regularly track key performance indicators (KPIs) such as order cycle time, inventory accuracy, and on-time delivery, and use this information to identify opportunities for improvement.As the industry continues to evolve and adapt to changing consumer demands and technological advancements, fulfillment is expected to be characterized by increased automation, omnichannel distribution, instant delivery, sustainable practices, and data-driven decision making.[hubspot type="form" portal="25799159" id="cd1c9ec1-2b99-42c3-9c0b-306be6b94bfb"]